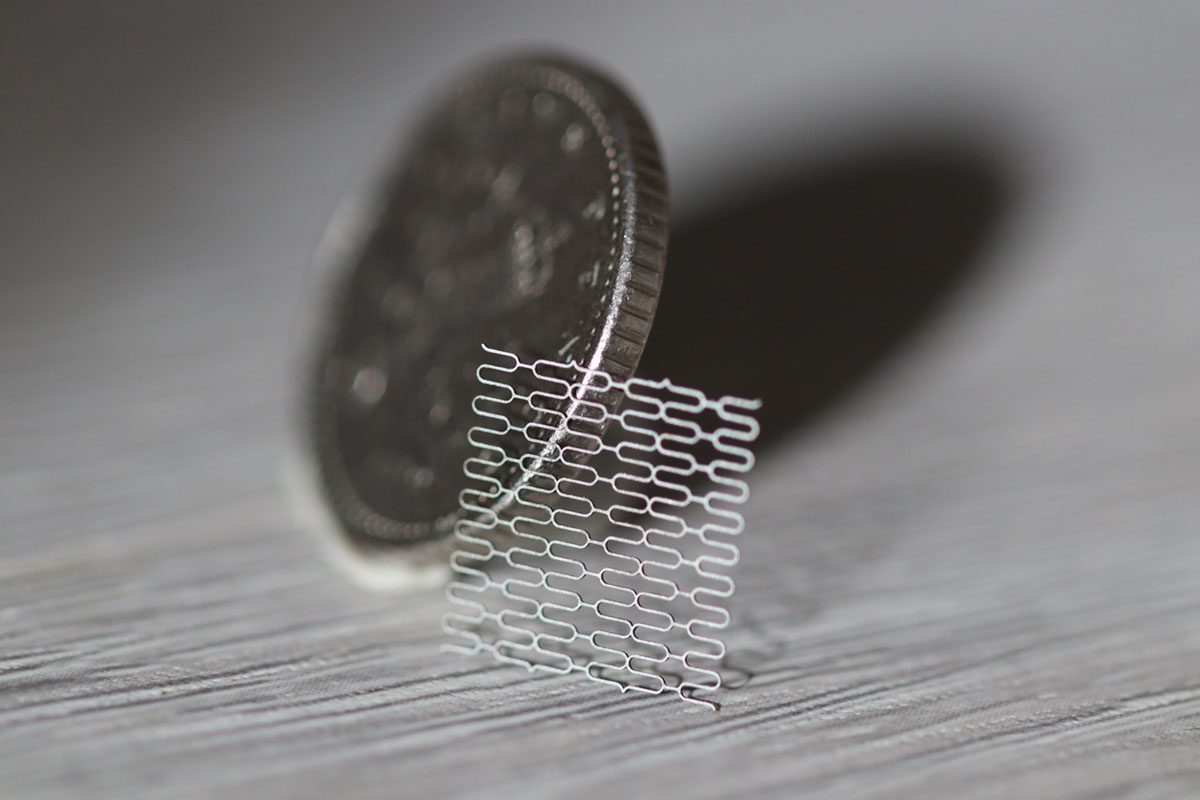
Nitinol is a highly unusual metal alloy of Nickel and Titanium. You can bend, twist, and crush it out of shape, only for it to jump back into its original shape when heated or submerged in hot water.
It possesses extraordinary super-elasticity and can survive repeated compressions and levels of repeated strain, whereas an equivalent piece of stainless steel will have long succumbed to fatigue.
Nitinol is nontoxic and does not promote genotoxicity, thus making it widely suitable for long-term medical implants.
The super-elastic properties of Nitinol coupled with its excellent biocompatibility means it has been the metal alloy of choice for demanding medical applications since the late 1980s.
Early medical uses of Nitinol include bone anchoring, tumor localization of specific cancers, and filter implants to trap and manage blood clotting. It is now widely adopted, with growing use, in minimally invasive surgery and dentistry.
The expected market growth for Nitinol in the medical market is expected to grow at over 9% CAGR, driven by improved therapy of chronic diseases and a preference for minimally invasive procedures. Nitinol is well suited to meet these needs.
Stents as an alternative to open surgery
Stents made from Nitinol are used to reinforce strictures within various ducts and canals of the human body caused by trauma or chronic medical conditions.
The use of stents negates any need to perform grafts or bypass surgery which makes it a highly desirable alternative to open surgery, where risks of secondary infection are higher.
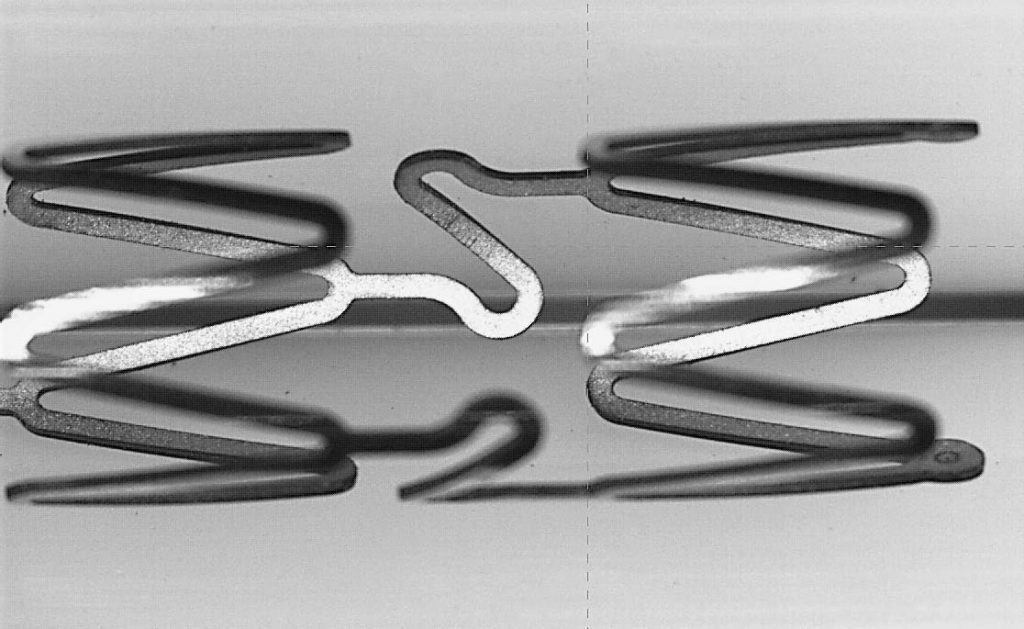
Minimal thermal impact
Ultrafast lasers are a natural choice to machine Nitinol stents and are widely used for this purpose. The near-diffraction-limited optical beam delivery yields a focused spot size optimized to machine small features. The short pulse dynamics of ultrafast lasers machine the Nitinol with minimal thermal stress or damage to the substrate.
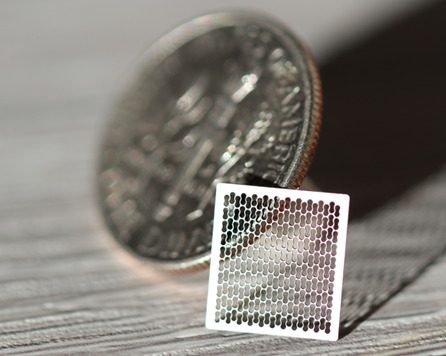
The test piece to the left shows the result of machining Nitinol with feature sizes consistent with an arterial stent. It was machined using our aeroPULSE FS50 laser using a single pass.
The laser beam was delivered using a commercially available processing head with an axial jet with a suitable cover gas to suppress oxidation and manage the generated plasma.
The results were an excellent simulation of the feature size and typical thickness of stents. The side walls are less than 65 µm and the feature sizes are <300 µm.
What lasers to use for Nitinol cutting?
The aeroPULSE FS50 is an ideal laser for cutting Nitinol. The combination of near-perfect beam quality, pulse energy and repetition rate selection means that it can cut delicate features such as arterial stents but can also process larger stents or bulk Nitinol at higher speeds due to the option for higher repetition rate and average power.
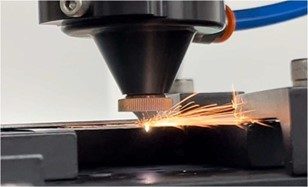
The aeroPULSE series of lasers is based on our photonics crystal fiber technology. As a result, it is an extremely reliable laser system ideal for industrial or scientific use. The FS50 is also used for cutting-edge neurostimulation research.
The ORIGAMI XP-S is also a strong candidate for Nitinol machining. Its excellent beam quality and high pulse energy are perfect for cutting fine features into Nitinol. The ORIGAMI laser is a diode-pumped solid-state laser architecture with a proven medical pedigree. It is used in a variety of biomedical applications, including ophthalmic laser surgery.
Both the ORIGAMI XP-S and the aeroPULSE FS lasers can be converted to different wavelengths via additional wavelength conversion units, which extend the range of materials they can process.
Both lasers also benefit from NKT Photonics’ powerful Software Development Kit (SDK), which can be used to independently control almost all laser output parameters.
Using the SDK, the laser, scanners, and stages can be automated to work together, enabling rapid research or production optimization. Both laser sources are ideal tools for basic R&D or full-scale volume production.